3D-ProSim
Innovative Robot Programming and Process Simulation
In today’s production, robot programming is often still carried out by teach-in or manually guided teach-in. Both methods require a high level of expertise, are time-consuming and can only be carried out directly on the robot while production is at a standstill.
3D-ProSim offers the solution thanks to intelligent offline programming. Based on his process knowledge, the operator determines directly on the 3D model of the part how the tool should impact it. This is done via so-called teach points and the process doesn’t require programming knowledge. Based on the teach points, 3D-ProSim calculates the optimum processing trajectory, taking into account the feasibility and process time of the program. The final robot program contains both movement commands for the robot and specifications for the control and use of the tool (e. g. dosing specifications for coating processes).
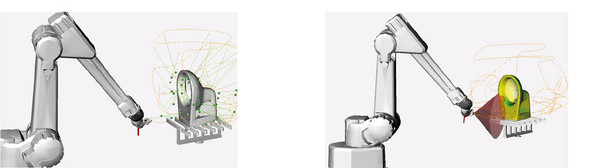
Features
- Offline robot programming outside the running production
- Fast and uncomplicated creation of optimized robot trajectories
- Simulation and visualization of the processing result for coating tasks
Advantages
- Substantial savings of glazing / painting material through optimized robot trajectories
- Transferability of programs created with 3D-ProSim to all common robot types
- Easy to learn and operate due to optimized workflows
File format for 3D models | WRL (VRML2) |
Origin of 3D models | From 3D scan or CAD |
Supported robots | Kawasaki, KUKA, ABB, Motoman, Fanuc, more on request |
Generation of trajectory | Fully automatic for 7 axes |
Robot program generation | Fully automatic for robots specified above |
End positions of axes | Adjustable with error message when limit is exceeded |
Axis velocities and accelerations | Adjustable with error message when limit is exceeded |
Predefinable glazing parameter sets |
20 |
Simultaneously usable glazing parameter sets |
Max. 8, depending on used glazing control |
Interface languages | German, English or Polish, more on request |