QuickSteps®
Fault Diagnosis and Identification of Measures in Case of Incidents
Modern production systems are characterized by the interdependence of individual processes. Therefore, errors in one process can shut down entire production lines, leading to high losses. Reducing the machine downtime caused by incidents is a key factor in increasing plant effectiveness (OEE). For that reason, incidents and their remedial measures must be managed. The challenge is centralizing, maintaining and retrieving information.
QuickSteps® provides the ideal solution: The worker on the shopfloor is guided through a series of dialogue queries for incident specification and is then shown the appropriate instructions for action. If an incident is not yet recorded in the software, the worker can easily document the measures taken. Therefore, QuickSteps® is a powerful tool for knowledge management (ISO 9001:2015) and supports a continuous improvement process.
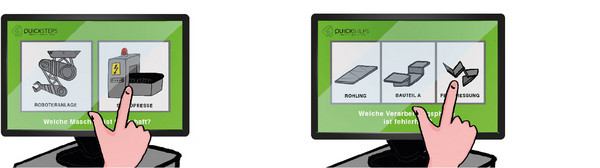
Features
- Straightforward selection dialogues, yes/no questions and image dialogues lead to quick incident specification
- Optimized for touch screen operation
- Comprehensive and central knowledge base for instructions for troubleshooting
Advantages
- Efficient tool for maintaining, protecting and accessing critical organizational knowledge (ISO 9001:2015, Clause 7.1.6)
- Increased OEE through reduction of downtimes caused by incidents
- Lower training costs for inexperienced/low skilled staff