Störungsassistent 4.0
Entwicklung eines assoziativen modellbasierten Assistenzsystems zur kooperativen Störungsanalyse und Fehlerbehebung am Beispiel Metall-Schutzgasschweißen
Zielstellung des Projektes
Im Projekt Störungsassistent 4.0 wurde das Ziel verfolgt, geeignete Methoden und Werkzeuge zur Erstellung eines assoziativen Assistenzsystems zur Erkennung und Fehleranalyse anhand der Beispielanwendung des Metallschutzgasschweißprozesses zu entwickeln. Zur Reduktion von Stillstandszeiten in Produktionsumgebungen besteht ein Bedarf an Systemen, die eine Wissensakkumulation über anlagen- und prozessspezifische Details mit Möglichkeiten zur Zustandsbewertung kombinieren. Hierdurch kann unabhängig vom Erfahrungsstand des Bedienpersonals eine schnelle Zuordnung von Fehlerbildern zu Handlungsanweisungen erfolgen. Im Bereich der schweißtechnischen Fertigung sind solche Assistenzsysteme bislang nicht verfügbar, da aufgrund des hochkomplexen Prozessverhaltens bislang kaum automatisierte Prozessbewertungsansätze verfügbar sind.
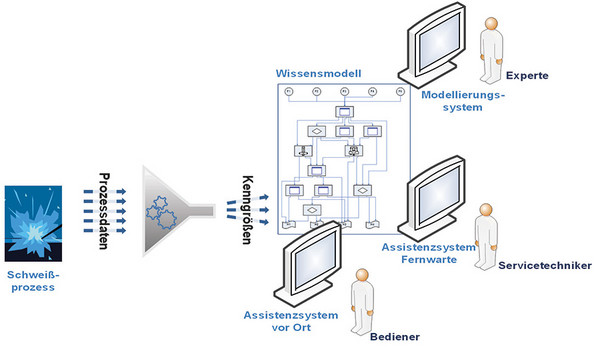
Projektergebnisse
Im Rahmen des Forschungsprojektes wurde ein assoziatives modellbasiertes Störungsassistenzsystem zur Unterstützung von Anlagenbedienern bei der Fehlerbehebung in der schweißtechnischen Produktion entwickelt. Hierzu wurden auf Basis von Prozessdatenanalyse charakteristische Merkmale der unter- suchten elektrischen Signalverläufe extrahiert und kategorisiert. Im nächsten Schritt erfolgte eine Kategorisierung von Störursachen. Anschließend wurde ein Meta-Datenmodell entwickelt. Über das konnten charakteristische Prozesskenngrößen an das Assistenzsystem übertragen und so auswertbar gemacht werden. Über die Entwicklung eines gekoppelten Assistenzsystems wurde die Struktur für eine Demonstratoranwendung geschaffen, die den Einsatz physisch getrennter Systeme zur Speicherung der Wissensdatenbank, der Aufnahme und Auswertung von Prozessdaten sowie der Benutzereingabe erlaubt und so den Beispielfall einer Fernwartungssituation darstellt.
In das entwickelte Konzept wurden in einem weiteren Schritt initiales Schweißprozesswissen sowie Fehlermodelle für die Schweißprozessdatenauswertung implementiert, um anschließend eine Validierung des Systems vornehmen zu können. Hierzu wurde eine typische Anlagenkonfiguration für die automatisierte schweißtechnische Produktion ausgewählt und anhand eines typischen Beispielbauteils validiert.
Auf Basis der Arbeiten in dem Projekt stehen KMU eine leistungsfähige Plattform zur Integration in reale Produktionsumgebungen zur Verfügung. Die Entwicklung eines Systems für reale Anwendungsfälle ist aufgrund der im Projekt geleisteten Methodenvalidierung nun gut realisierbar. Zudem können bereits zum jetzigen Zeitpunkt die Hersteller von schweißtechnischen Überwachungssystemen sowie die Hersteller von Schweißstromquellen die gewonnenen Erkenntnisse direkt für die Weiterentwicklung ihrer Produkte einsetzen.